The basic principles of disinfection and biosecurity have a long history in animal production. For aquaculture, these terms are also frequently used, and several protocols are applied in some aqua species.
The variation in the application of disinfection and biosecurity protocols is because of the huge diversity in aquatic species, each requiring a different biosecurity program tailored to the specific environment and the pathogens affecting that aquaculture system.
The aquaculture industry is less mature compared with livestock production systems, and this means that the basic concepts of biosecurity and disinfection are out of date or have a poor application level in some species. As an example, the biosecurity, sanitation, and disinfection protocols used in salmonid production are very different to those applied in carp production.
It is well known that a complete and efficient sanitation and disinfection program cannot be achieved using a single product. This is because there are several variables (Scarfe et al., 2006) including:
- degree of microbial killing required
- devices and equipment to treat
- types of surfaces
- costs
- safety
- availability of hygiene products
In 2012, Yanong and Erlacher-Reid described biosecurity in aquaculture as a set of practices which minimise the risk of introducing and spreading an infectious disease to the animals at a facility, and which minimise the risk that diseased animals or infectious agents will leave a facility and spread to other places and to other species. These practices also potentially reduce stress to the animals, thus making them less susceptible to disease (Yanong and Erlacher-Reid, 2012).
The differences between sanitation and disinfection may be confusing in aquaculture. In the main production regions, most producers perform some disinfection but with poor cleaning procedures. Cleaning must be the first action aiming to remove all foreign material like organic matter and biofilms. The second phase is disinfection where the goal is to eliminate as many pathogenic organisms as possible (Yanong and Erlacher-Reid, 2012).
It is important to note that the cleaning and disinfection procedures and their effectiveness varies between the stages of the culture. For instance, the disinfection of one hatchery or nursery facility will be easier in comparison with an earthen pond where fattening is carried out. In an earthen pond, a complete disinfection is not possible.
Biofilms in hatcheries and nurseries
The results of inefficient cleaning and disinfection are sometimes evident at the very beginning of the culture (Figure 1). For instance, in shrimp larvae production, a high level of mortality can be caused by some species and strains of Vibrio. There is dated evidence of the presence of Vibrio biofilm on different surfaces like cement, liners (HDPE) and steel. It is also well known that a Vibrio harveyi biofilm has a strong resistance to sanitiser chlorine and is even resistant to antimicrobials such as chloramphenicol and tetracyclines (Karunasagar et al., 1995).
Other groups of bacteria which form biofilms and affect aquaculture productivity, and especially fish production, are the Aeromonas group. Biofilm formation depends on environmental conditions such as temperature and nutrient availability (Chenia and Duma, 2016).
Nowadays, sanitiser chlorine is widely used in routine disinfection procedures in most places. All concrete tanks, utensils and general structures are usually inefficiently treated with a solution of sodium hypochlorite (NaOCl), where prolonged use can cause resistance development.
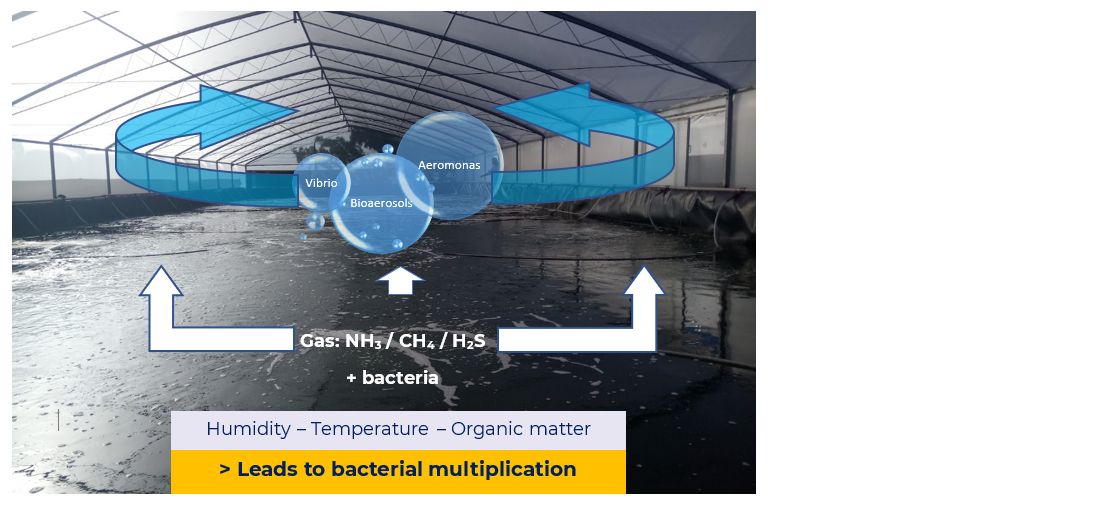
Biofilms can also establish in water pipelines and sometimes the protocols to remove them are not sufficient to ensure complete disinfection. The structure of the pipeline must be planned in such a way that makes disassembly easy in order to ensure appropriate sanitising and disinfection of all sections.
Biofilms and their importance in aquaculture
Inefficient sanitation and disinfection protocols can lead to high mortality and low productivity levels due to the infection pressure which remains after each production cycle. In summary, biofilms and bacteria can:
- reduce disinfectant activity
- develop resistance against chlorine and other disinfectants
- transmit disease from hatchery and nursery structure to animals
- reseed systems and animals after the sanitary break
- cause contamination from air pipelines and blowers
- cause contamination of filters, pipes and aeration systems
- accumulate over several production cycles
- have a high infection level even at the beginning of the cycle
- lead to mortality and economical losses
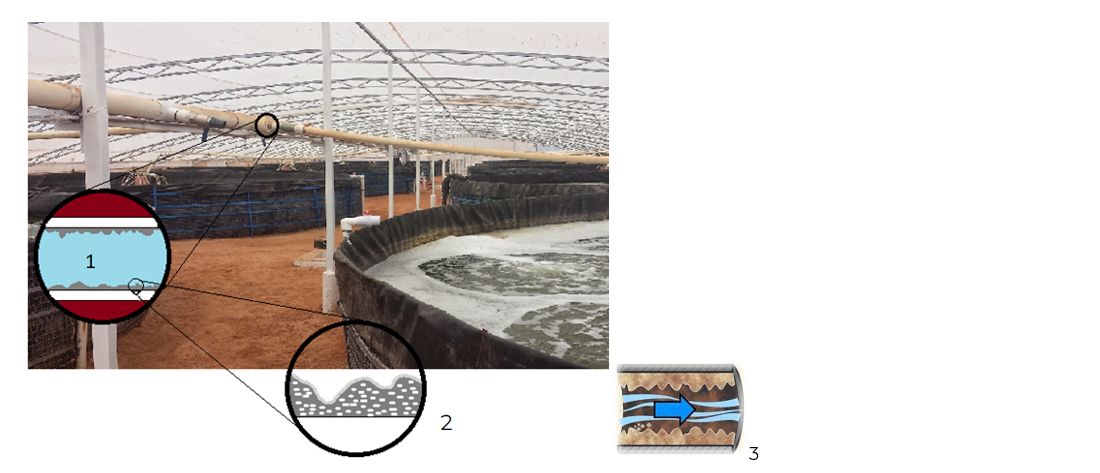
Efficacy of Prophyl® S and Vulkan® Max in hatcheries and nurseries
To prove the efficacy of Huvepharma's portfolio of hygiene solutions in hatcheries and nurseries for fish and shrimp, we tested the efficacy of Prophyl® S and Vulkan® Max against the 10 main pathogenic bacteria in aquaculture (Table 1).
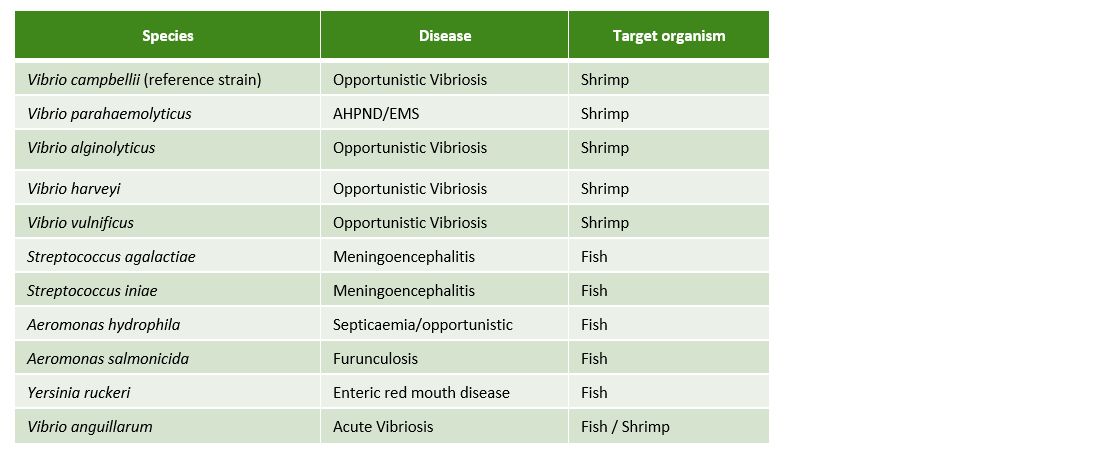
Antibacterial activity
We investigated whether the tested products could prevent growth (bacteriostatic activity) and kill (bactericidal activity) diverse shrimp and fish bacterial pathogens in vitro. To evaluate bacteriostatic activity, we used a liquid interaction setting called the minimum inhibitory concentration (MIC). Subsequently, for evaluating bactericidal activity, we used a solid interaction setting called the minimum bactericidal concentration (MBC).
- Minimum inhibitory concentration (MIC)
The bacteriostatic activity of the tested products against the bacteria was determined using a minimum inhibitory concentration (MIC). This protocol was based on a broth microdilution method and followed the NCCLS guidelines (M31-A2).
- Minimum bactericidal concentration (MBC)
In order to investigate whether the tested products demonstrated bactericidal activity against the bacteria, a minimum bactericidal concentration (MBC) procedure was performed. Based on the MIC results, three concentrations were chosen to be plated onto agar plates: the MIC value and two higher concentrations. After the overnight interaction of the products and bacteria, samples were spread onto agar plates of the same media and the plates were then incubated for 24-48 hours at 27 oC.
The MBC was determined by the absence of bacterial growth on the agar plates.
Results and discussion
The MIC study was quantified in a liquid medium aiming to simulate a situation where the tested products interact with pathogens in liquid phases such as digestive fluids or seawater. The MIC is a direct but inverse measure of the power of the tested product's bacteriostatic activity against shrimp and fish pathogens. The lower the MIC, the higher the inhibiting power of the tested product. In addition, the MIC and where possible, two higher concentrations were further plated to evaluate the bactericidal effect of the tested product. This resulted in the reported MBC.
In order to confirm the correct execution of the MIC test, the antibiotic gentamycin was used as a positive control. The activity of gentamycin against V. campbelii (positive control) showed inhibition at the expected concentration of 4-8 mg/L. The control plate for bacterial growth (with no antibacterial product) showed normal growth for all bacteria, and the control plate for bacterial contamination of the culture medium did not show any bacterial growth. The results of these control treatments confirm the correct execution of the current MIC test.
Prophyl® S
The results presented in Table 2 and Figure 3 demonstrate that Prophyl® S showed an MIC ranging between 93.75 mg/L (Streptococcus spp.) and 750 mg/L (Vibrio spp. and Y. ruckeri). On the other hand, the values of the MBC varied from the MIC depending on the microorganism.
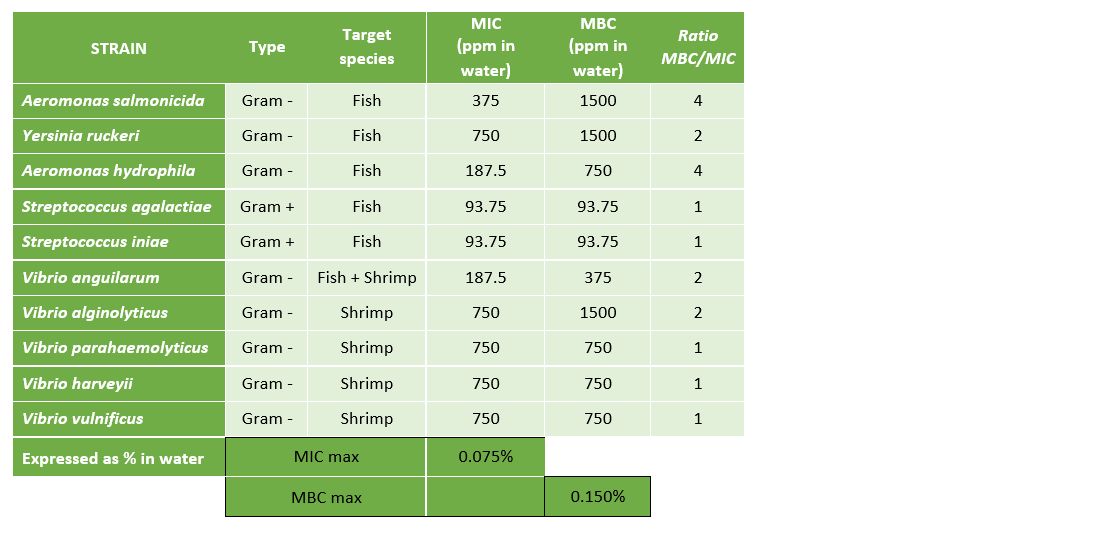
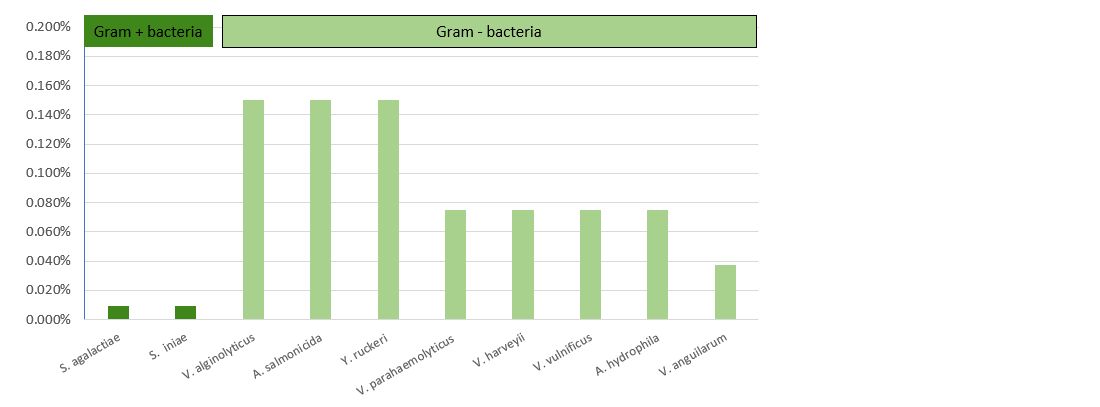
Vulkan® Max
The results presented in Table 3 and Figure 4 demonstrate that Vulkan® Max showed an MIC ranging between 23.44 mg/L (Streptococcus spp.) and 187.5 mg/L (Vibrio spp.). The values of the MBC and MIC were the same for each pathogenic microorganism.
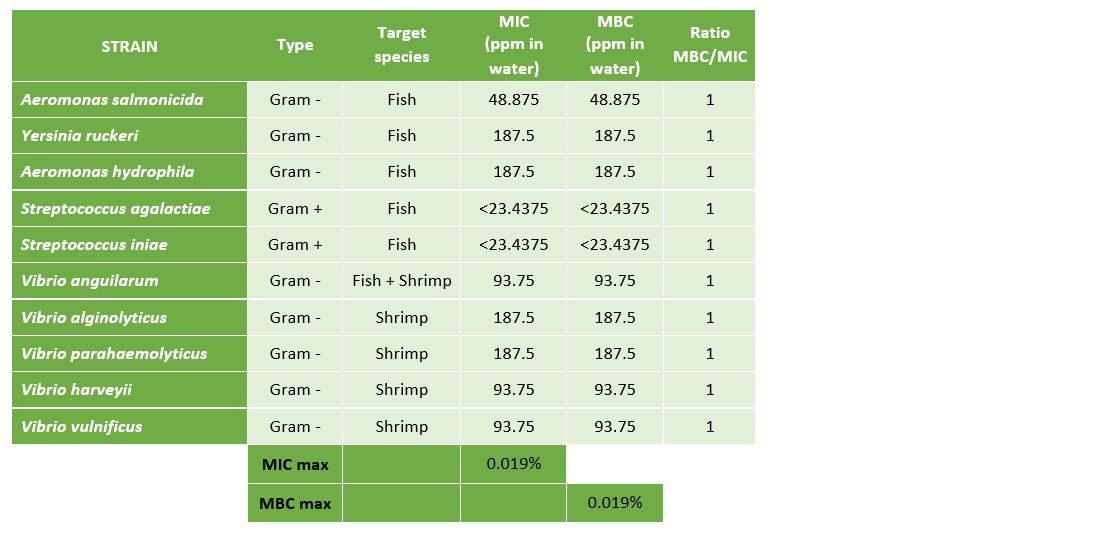
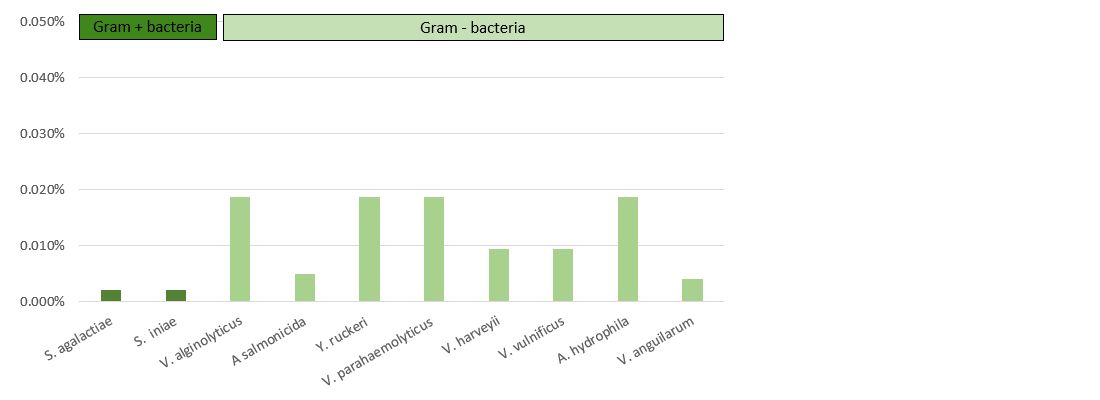
Conclusions
- A high bacteriostatic / bactericidal activity was demonstrated for both Vulkan® Max and Prophyl® S for almost all the tested pathogens.
- Vulkan® Max and Prophyl® S demonstrate good bacteriostatic / bactericidal activity against shrimp pathogens: AHPND / EMS and Opportunistic Vibriosis.
- Vulkan® Max and Prophyl® S demonstrate good bacteriostatic / bactericidal activity against fish pathogens: Meningoencephalitis, Septicaemia, Furunculosis, Enteric red mouth disease.
- The MIC values for Vulkan® Max and Prophyl® S against all pathogens were better than the expected range (600 - 1000 mg/L) for regular products with bacteriostatic activity.
References are available on request