Aquaculture activities are located mainly in rural or remote areas where the environmental conditions are not largely affected by humans and the demand for land for other activities such as tourism or industrial developments is low.
Excluding the salmonids, most farmed fish and shrimp are produced in the tropical regions of Southeast Asia and Latin America. According to the last FAO aquaculture report (2022), aquaculture is expected to expand mostly in the Americas (up 29% from 2020), Africa (up 23%) and Asia (up 22%). The growth in Africa's aquaculture production will be driven by the additional culturing capacity put in place in recent years, as well as by national policies promoting aquaculture fuelled by rising local demand because of higher economic growth. In the meantime, Asian countries will continue to dominate the aquaculture sector, maintaining their share of 88% of 2030 global aquaculture production and being responsible for nearly 90% of the increase in production by 2030 (FAO, 2022).
Logistics of enzyme use
Producers of aquatic feed are also strategically located in geographical areas that allow them to cover markets and deliver products to farms in a short time. Feed mills need to be adapted to managing a complex process for the import, transport and storage of all the ingredients and additives used in their formulations.
For some tropical regions, the use of liquid enzymes delivered in IBCs is a viable alternative. However, in other major producer countries, the stability of these liquid enzymes may be compromised, in particular when temperature-controlled transport and storage is required.
The current global situation includes massive delays in sea freight transport, as well as the common logistic problems faced in countries without a solid customs structure. These factors lead to disruption in the availability and quality of feed additives that require control of temperatures. It is particularly important to consider delivery time with regards to the shelf life of the enzyme to ensure optimal enzyme activity. In the case of liquid enzymes, shelf life is typically one year.
Instant water-soluble enzyme powders
The basis of this concept is quite simple: why not produce liquid enzymes in the feed mill itself? This was the question which led to the development of the Huvematic® by Huvepharma®.
This concept has two elements:
- The development of water-soluble enzyme powders (WSPs)
- The development of a tool to automatically produce liquid enzymes on demand at the feed mill
Huvepharma®'s knowledge and experience in the production and processing of enzymes led to the development of a range of instant water-soluble enzyme powders (WSPs) including Hostazym® X WSP (NSPase) and OptiPhos® WSP (phytase). These products are 50 - 150 times more concentrated than the usual available enzyme powders and are soluble, even in cold and hard water, within 30 seconds.
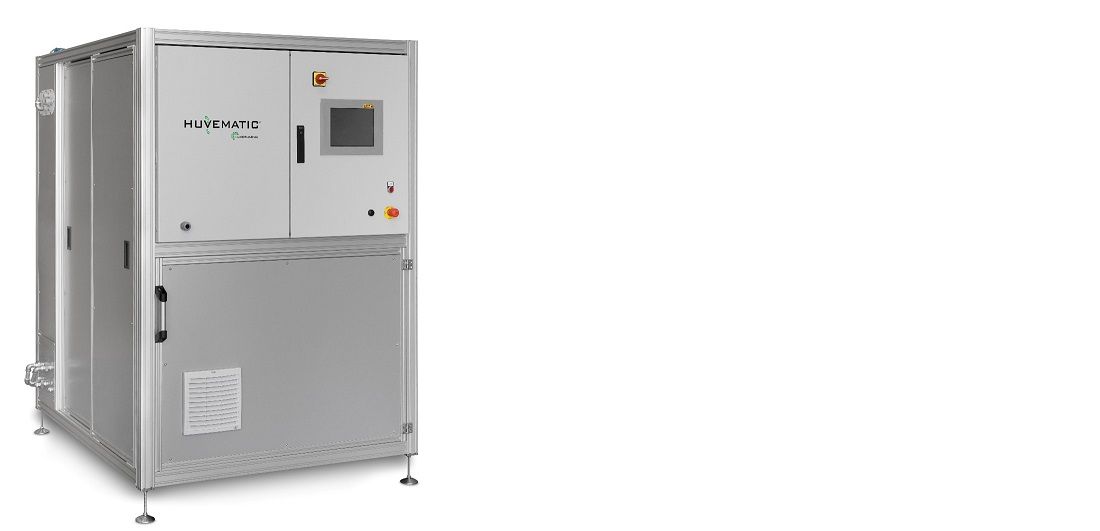
A machine called the Huvematic® (Figure 1) automatically produces liquid enzymes from the WSP powders (Figures 2a and b). This machine accurately weighs the required quantities of WSP enzymes and water and mixes them together so that the liquid enzyme is produced at precisely the required concentration. The Huvematic® produces batches of 5 to 15 litres and can be fully integrated into factory production. It can operate automatically and includes a reporting system to fully comply with the regulatory quality control and traceability standards. One Huvematic® has enough production capacity to serve multiple post-pelleting liquid application (PPLA) lines within the same feed mill.
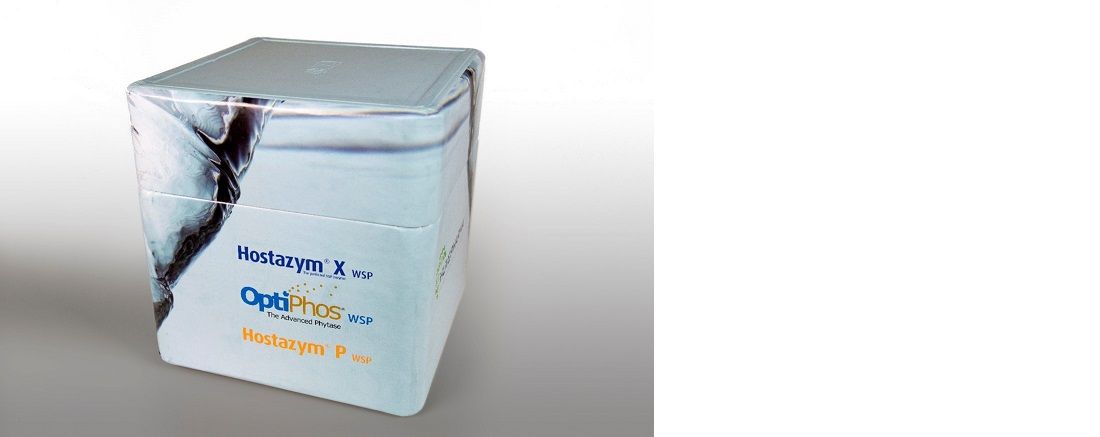
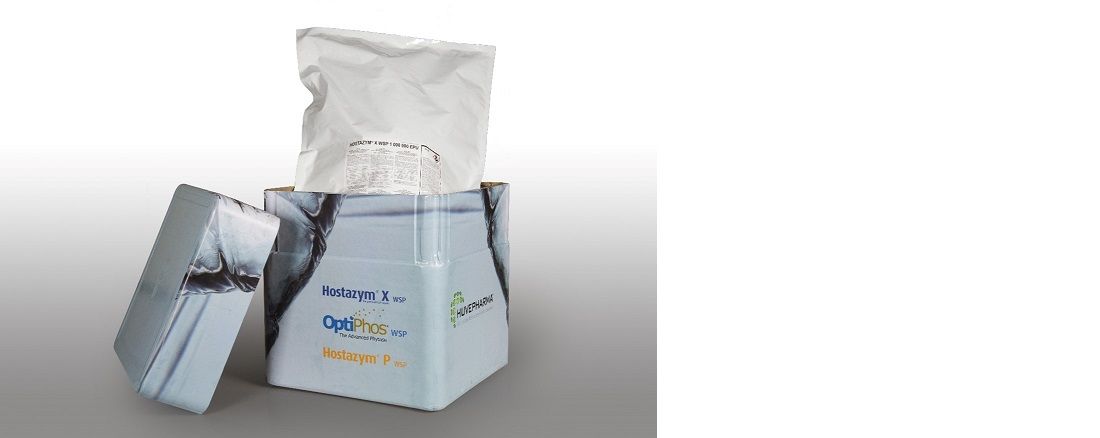
Worldwide implementation
This innovation by Huvepharma® is new in most areas of the world. However, it has already been widely accepted for more than seven years in the US where it is intensively used for land animal species. For aquaculture applications, the Huvematic® can help to meet the increasing demand for enzymes to be used in functional feeds. This success has encouraged Huvepharma® to launch the concept of WSP enzymes globally for the aquaculture industry.
Major benefits of the Huvematic®
The feedback obtained from some key players on the Huvematic® and our WSP enzymes include:
- Daily production of fresh liquid OptiPhos® phytase - based on highly concentrated WSP (water-soluble powder containing 750,000 FTU/g)
- Flexibility in phytase dosing - Huvematic® programming can be adapted to optimise the concentration of the liquid phytase produced
- Flexibility in adapting spraying volume - the Huvematic® system allows the phytase and/or water volume during spraying to be changed
- Saving in cool storage room space compared to existing liquid enzyme storage - cool storage can be used for other goods
- Saving on enzyme cooling needs at site - resulting in savings on energy costs
- Decrease in enzyme carbon footprint - recent outsourced calculations show a massive reduction in the CO2 footprint of our WSP OptiPhos® product compared to a liquid enzyme (transported as a liquid as currently done)
- Simplification of logistic efforts - volumes involved are divided by a factor of 75 and highly concentrated WSP enzymes can be air shipped
- Increased safety and reduced risk of human errors - the Huvematic® is a fully automated system
- Innovative and sustainable solution for feed enzyme application - the Huvematic® machine produces fresh liquid enzyme on-site with a total carbon footprint reduction of 80% compared to a liquid enzyme.
Conclusions
The Huvematic® assures the correct application of liquid enzymes in countries with logistic challenges.
WSP enzymes are the more convenient type of enzyme for aquatic feed mills, minimising logistic and quality problems.
The Huvematic® is the most convenient tool to deliver fresh enzymes produced in situ and avoids thermic expositions and loss of efficacy during transport and storage.
References are available on request