Selecting an enzyme is a strategic decision that assures optimal animal performance with a cost-effective outcome. Especially in the current market of high raw material prices, enzymes are in the spotlight as a feed cost-saving tool.
Alongside nutritional strategies, the chosen enzyme needs to endure processing challenges related to feed production. Enzymes must remain stable during conditioning and pelleting. It is known that the processing stability of enzymes is influenced by numerous factors, such as temperature, time, moisture, pressure, die and feed formulation, to name but a few. The multiple ways in which these factors can combine are critical to a clear understanding of the enzyme's processing stability.
Equally important is an understanding of the influence on enzyme stability of each feed plant. Each feed plant is different and has its own specific equipment, work processes, sampling procedures and even personnel, all of which are variables that will contribute to determining enzyme stability.
Understanding all the variables is key to be able to assess the stability of a product and determine the acceptance criteria from the analytical results for a specific production site. The multiple variables involved means that one result or one test will not tell you much about the processing stability of an enzyme because information on industrial process variation is lacking.
Making a fair assessment of the stability of any molecule passing through an industrial process takes time, needs repetition, a large data set and some statistics. The enzyme's processing stability and the acceptance criteria for laboratory recovery results require analysis. The most reliable tools are time and data. Following the use of quality control tools to analyse the results, specific conformity criteria can be compiled or it can be decided whether or not an enzyme is suitable for a specific production unit.
What do the recovery results tell us?
Multiple research and field trials were conducted to assess the processing stability of the enzyme Hostazym X, a non-coated enzymatic complex, xylanase based. Overall, the results support the label claim: "stable in pelleting processes up to 85oC". However, it should be stressed that generalisation cannot be applied to enzymes and processing stability needs to be evaluated on a case-by-case basis.
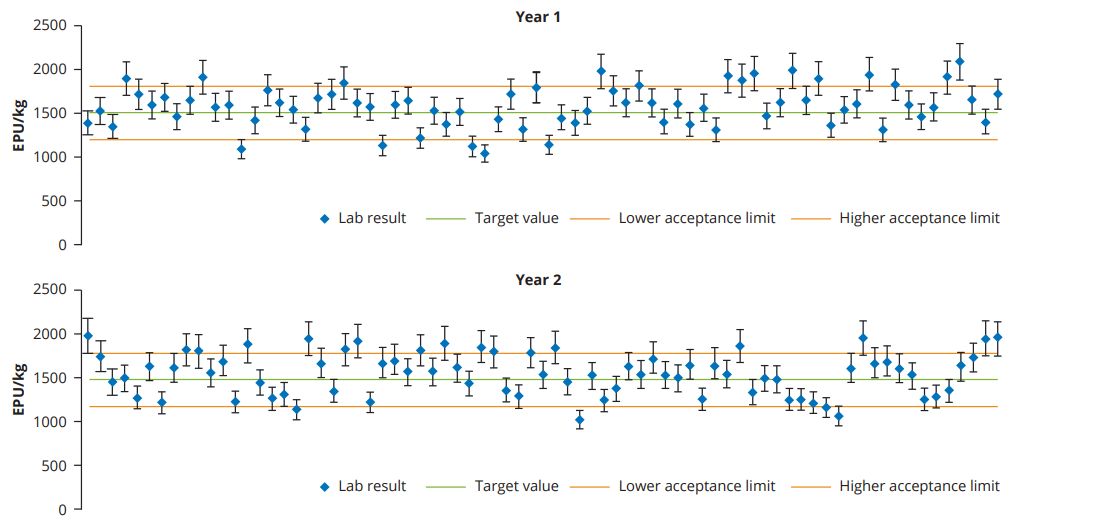
To illustrate the importance of on-site evaluation of enzyme stability, the control charts from an actual feed plant are shown in Figure 1. The selected feed plant belongs to a company with multiple production sites, the data shown is from one of its production sites for broiler feed. The processing temperature reaches up to 88oC and the conditioning time ranges from 60 to 120 seconds. The enzyme, Hostazym X, has a target concentration in feed of 1500 EPU/kg of xylanase and the customer has established acceptance criteria for the laboratory recovery results of +/- 20% of the target feed concentration.
Control charts are a basic quality assurance tool for monitoring results and process variations, to decide on product conformity, identify trends and annual variances and, in this case, to validate that the enzyme is stable under the processing conditions of that specific production unit.
- Recovery results (Figure 1) show a 96% conformity rate
- The control chart alerts to off-specification results at specific moments where the causes and need for corrective or preventative measures should be evaluated. Of the 4% non-conformance results (higher or lower than acceptance limits) none was directly attributable to the product itself
- Analysis of data over the years can also help to identify improvement opportunities or be used to review conformity criteria in the production unit
In conclusion
- Enzyme processing stability involves numerous variables and the laboratory recovery result is a checking tool, part of a quality assurance plan
- The conformance / non-conformance criterion is a quality parameter specific to a production site
- Results vary and are expected to vary. Understanding the variation and assessing enzyme stability within the variation is a key decision factor when establishing conformity criteria
- Recovery results reflect a series of influences from production unit to laboratory, not just the product
- It is essential to understand that assessing a production unit and establishing quality assurance criteria takes time, data and close cooperation between customer and supplier