This has led to the development of tools to apply heat sensitive compounds to the feed after the heat treatment process, called post-pelleting liquid application (PPLA).
To feed the PPLA system with liquid enzymes at the feed mill, enzyme manufacturers need to produce the enzyme as a liquid, stabilise it by adding stabilising agents and conservatives, pack it in 1,000 litre Intermediate Bulk Containers (IBCs) and transport it to the feed mill where it is stored until the IBC is connected to the PPLA system for use. This complete process requires a stable and cool environment to guarantee the concentration of the enzymes in liquid form.
Working with liquid enzymes packed in IBCs has many downsides as enzymes in liquid form tend to be less stable than dry enzymes. An example of a stability study conducted with commercial available phytases on the market is shown in Figure 1.
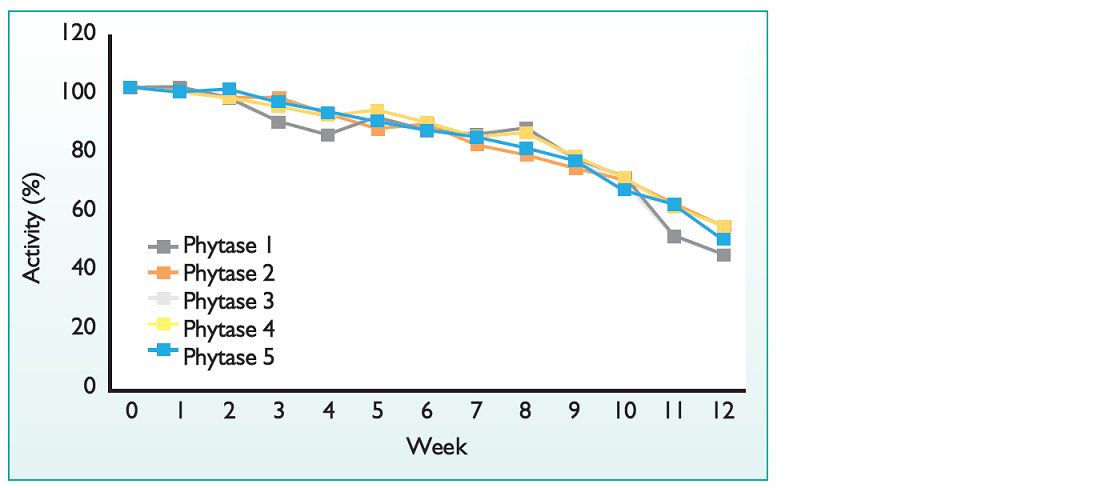
It can be seen that the enzyme activity of liquid phytase (in an IBC) decreases by up to 50% when stored for 12 weeks at 40oC. Therefore, IBCs with liquid enzyme require a lot of temperature controlled storage space and cooled transport. Next to this, the manipulation of the IBCs at the feed mill poses extra labour costs, often results in leakage or spillage, and takes up important stock inventory space.
Also the carbon footprint of this way of supplying enzymes is greatly reduced compared to shipping liquid enzymes.
WSP enzymes
The development by Huvepharma of instant water soluble enzyme powders (WSP enzymes) has opened the way to produce liquid enzymes freshly at the feed factory when needed.
With these WSP enzymes, liquid enzymes can be tailor made at the feed mill in any desired amount and concentration just prior to application with the PPLA.
For dissolving the WSP enzymes, special equipment has been developed: the Huvematic which allows the enzymes to be dissolved even in cold and hard water. The Huvematic weighs the desired quantity of WSP enzymes and the required quantity of water very accurately, and mixes them together so the liquid enzyme is produced at the right concentration.
The Huvematic can run to produce two enzymes at the same time (for example a phytase and an NSPase) and has enough production capacity to serve multiple PPLA lines in the same feed mill.
The dry WSP enzymes are commercially available under the brand names OptiPhos, Hostazym P and Hostazym X and are packed in boxes containing four aluminium sealed bags of 5 kg each. One box containing 4 x 5 kg of WSP enzymes can replace two or three 1,000 litre IBCs filled with liquid enzymes.
This innovation by Huvepharma is now well established, and is common practice for more than 5 years all over the world including Europe, US, Middle East and Asian countries proving its efficacy and operation security. Large broiler integrators have embraced the technology to avoid the challenges and inconveniences related to using liquid enzymes in IBCs (as described above), and were the pioneers of using this new technology and WSP enzyme products. The concept was initially introduced for using an in-line produced liquefied phytase (OptiPhos) and led to the installation of Huvematic in multiple feed mills.
Following the success of the early installations, Huvepharma extended the concept for the production and application of liquefied NSPase (Hostazym X) using the same formulation technology developed in their R&D laboratories. The concept of WSP enzymes is now available and well established globally. Local (country) registrations of the WSP enzyme were approved and collaboration with local companies to support Huvepharma with the installation, maintenance and related technical support of the Huvematic was established. The Huvepharma Global Industrial Service Manager is constantly supporting and monitoring the factories using the new Huvematic technology.
In hot and humid areas this concept has been welcomed with high enthusiasm. The challenging conditions like high temperatures and high humidity allowed the easy roll-out of the concept in South Asia, Middle East, the Pacific region and South America, solving the current difficulties with the IBCs regarding stability, activity and extra labour.
Conclusion
Instant water soluble enzyme powders (WSP enzymes) are a unique tool for the production of liquid enzymes on site, offering the nutritionist flexibility and security in formulation. Avoiding the need for IBCs, reducing cooled transport and storage conditions and their related costs, reducing labour costs involved with IBC movements at the feed mill, reducing waste and spoilage are additional benefits realised by the feed mill manager.
This concept has been implemented with success worldwide and provides a solid base of experience for future new installations.
Get in touch with a member of the Huvepharma team to find out more.