The pelleting process
During the pelleting process (Figure 1), mash feed is heated in a conditioner using steam to reach a given temperature. Dry steam is added at a steam injection point at a ration of 1% (1 kg/100 kg mash) for every 15oC increase in feed temperature as required. Final temperatures in the conditioner vary from 65oC to 90oC of even higher.
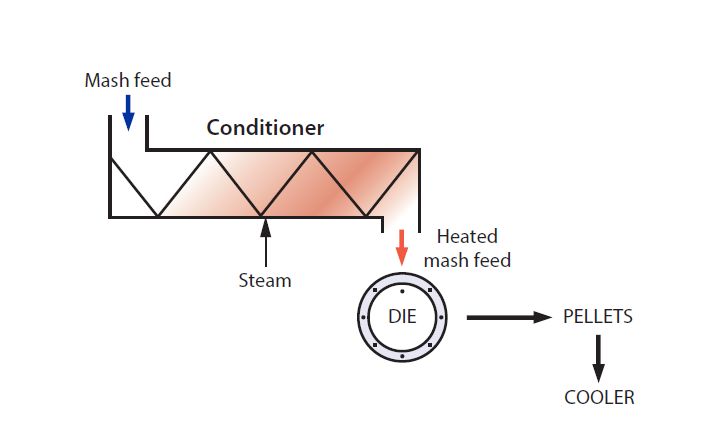
After the feed has been conditioned, it is compressed into a die (Figure 2) to form the pellet. This generates friction heat which increases the temperature of the pellets.
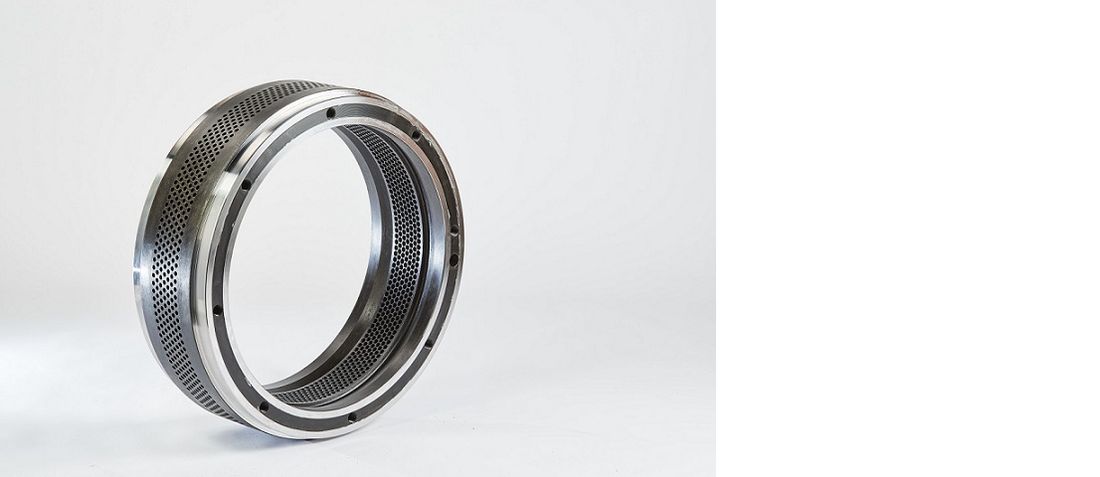
After die compression, the pellets are cooled with ambient air in a vertical counter-current cooler (Figure 3), where cold air is blown in from the bottom while pellets enter from the top. During cooling, the pellets are also dried. The final temperature is approximately room temperature while moisture content should be below 13%.
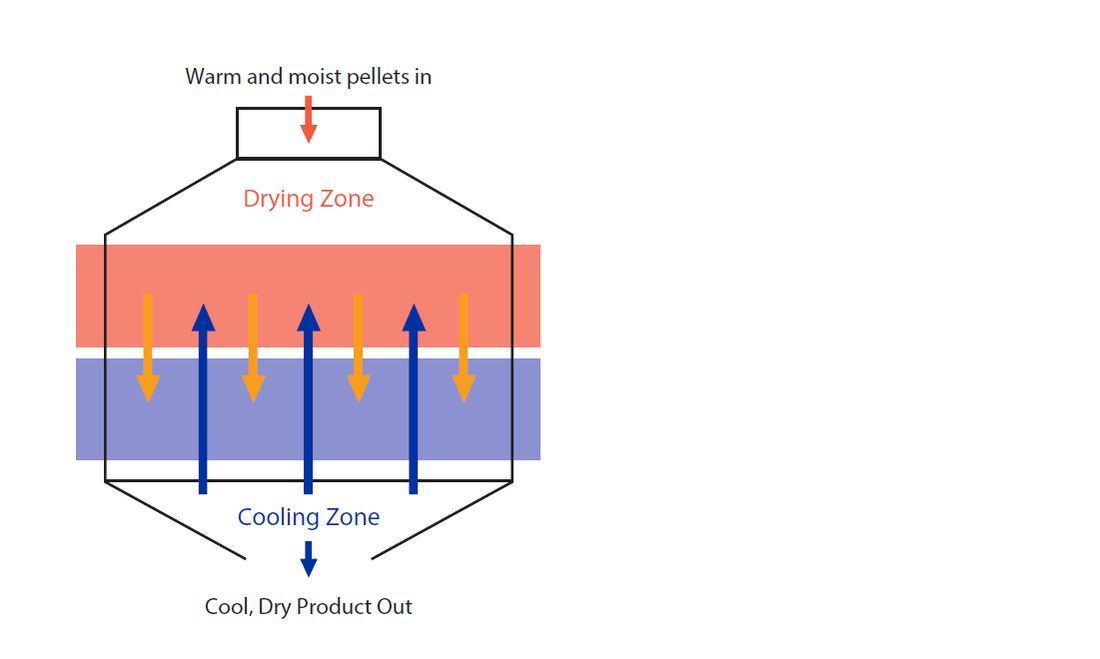
Processing factors affecting phytase recovery
Conditioning temperature and time
Phytase inactivation increases with temperature and time in the conditioner. Depending on the properties of the specific process, the conditioning system can vary from a short time (30 seconds, for example in a steam mixer) up to a hygienizer with an extended conditioning time (3 to 4 minutes).
Moisture content of the mash feed
Dry heat has a less negative effect than wet heat. Low quality steam (oversaturated steam containing water droplets) results in a higher feed moisture and thereby negatively affects phytase stability.
Diameter and length of the die
Die friction will increase the temperature of the surface of the pellets. Friction heat increases as die channels get longer and narrower, resulting in a higer phytase interaction. The length: diameter (L:D) ratio of a die is therefore an important parameter; the higher the value, the more friction heat can be expected. For monogastric feeds, die holes are normally 2 to 4mm in diameter and 40 to 80mm long. Small pellets (2mm) tend to show lower phytase recoveries than large (5mm) pellets. A higher throughput of feed also increases pelleting friction.
Feed composition
- Changing the protein and starch content of the feed has little impact on phytase recovery.
- Minerals and fiber negatively affect die throughput as they increase friction and thus negatively affect phytase recovery.
- An increase in free fat percentage results in a higher feed throughput (fat is a lubricant even at 0.5% in teh feed formula) and thus has a positive effect on phytase recovery. A recent trial conducted at Ghent University, Belgium investigating the heat stability of OptiPhos® Plus with different levels of added fat showed that phytase recovery can be 8% higher at 85oC when 3% fat is added, even with a prolonged (120 seconds) conditioning time (Figure 4).
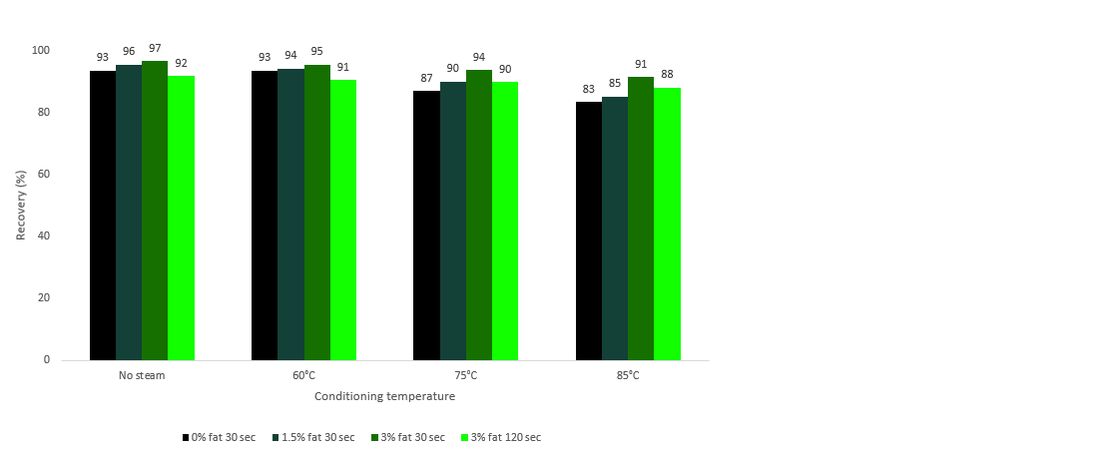
Cooling rate of pellets
The speed of cooling also determines phytase recovery. Slow cooling means a prolonged heat effect. A cooling (and drying) process in a counter-current cooler can take up to 15 minutes, but the temperature of the pellet in the cooler normally drops below 70oC quickly. Below this temperature, the impact of heat on phytase recovery is limited. However, inadequate speed of cooling the pellet can lead to increased losses of phytase activity. For instance, a study conducted at Ghent University, Belgium showed that inadequate (slow) cooling of pellets could negatively impact recovery results by 10% at 30 second conditioning and 3 bar steam pressure. Recovery was 17% lower with a prolonged conditioning time (120 seconds; Figure 5).

Conclusion
Determination of the recovery of a phytase during pelleting depends on many factors, including the desired heat treatment of the mash, the equipment, the steam quality, the feed composition, the pellet form and the speed of cooling. And finally, it also depends largely on the intrinsic heat stability of the phytase itself.